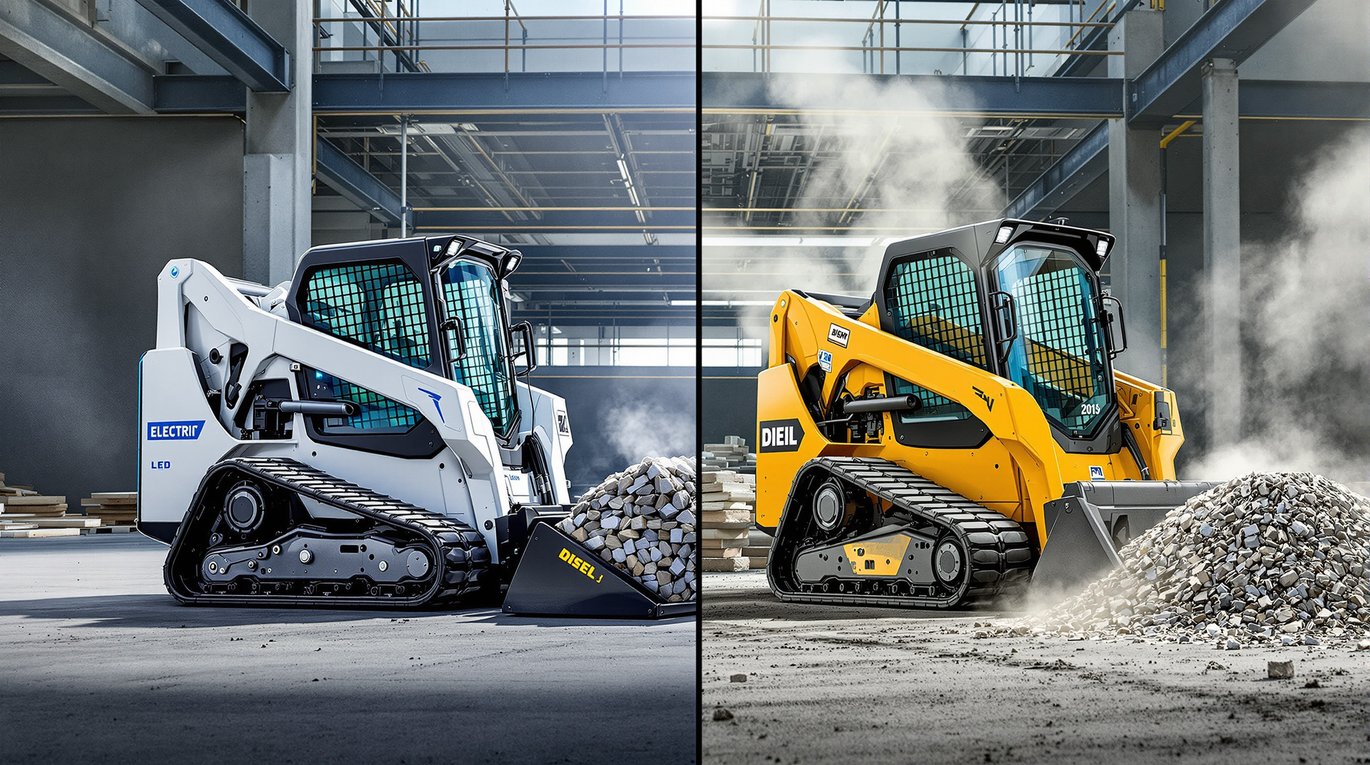
The construction industry faces a pivotal moment as traditional diesel-powered equipment competes with new electric alternatives. Equipment costs and environmental regulations continue to change, making professionals rethink their equipment choices.
Construction professionals show heightened interest in electric skid steer options lately. These machines offer zero emissions and run quietly, but questions linger about their ground performance when matched with diesel models.
This comprehensive comparison between electric and diesel models will give you the power specifications, operating efficiency, and technical capabilities of both options. You'll learn which skid steer loader fits your project requirements and work environment best.
Power and Performance Specifications
The power specifications between electric and diesel skid steers show fascinating differences in performance delivery. Let's examine the numbers that matter most.
The Bobcat T7X, a leading electric skid steer loader, packs 107 horsepower with instant torque that delivers three times more power than regular loaders. The diesel version, Bobcat S770, generates 92 horsepower.
These machines compare in performance metrics as follows:
Specification | Electric T7X | Diesel S770 |
Rated Operating Capacity | 2,900 lbs | 3,350 lbs |
Travel Speed | 7.8 mph | 12.3 mph |
Operating Weight | 11,970 lbs | 9,314 lbs |
Operating time varies between these machines. Diesel versions run approximately 20 hours under load with a full tank. The T7X electric model runs 4-6 hours on a single charge. The runtime increases by a lot during intermittent use throughout a workday.
Electric models offer several advantages:
- No lag power delivery while running multiple functions
- Quiet operation at just 65.4 dB from the operator's position
- Zero emissions during operation
- Smart power management extends battery life
A 72.6-kilowatt-hour lithium-ion battery system powers the T7X's drive system and controls lift and tilt functions through electric actuators instead of traditional hydraulics.
Operating Efficiency Analysis
My analysis of electric and diesel skid steers shows some eye-opening differences in how they operate. Let me share what I found about their real-life performance.
Electric skid steers beat diesel ones by a lot in maintenance needs. Take the Bobcat T7X - it runs with half the parts and needs 96% less fluid than diesel models. You won't need oil changes, filter replacements, or DEF management. These savings add up fast.
The cost comparison tells an interesting story:
- Annual energy costs for 750 operating hours with an electric skid steer: USD 810.00
- Annual fuel costs for 750 operating hours with a diesel skid steer: USD 12,960.00
Runtime needs careful planning. The Elise 900 electric skid steer runs about 6 hours under load with its biggest battery option. You'll need to plan your charging schedule since it takes around 3 hours to reach 80% charge on a 240V outlet.
Something that caught my attention was how electric models eliminate idle time waste. Diesel machines burn through 0.5 to 1 gallon per hour while idling. Electric versions use no power at all when they're not moving. This feature saves money because machines typically sit idle 50-60% of the time.
Charging setup needs some thought. Operators need Level 1 (120V) or Level 2 (240V) charging access. A full charge takes up to 24 hours with Level 1, but Level 2 charging cuts this time by a lot.
Technical Capabilities Assessment
The technical architecture of electric skid steers shows some amazing features that make them different from diesel models. The Bobcat T7X breaks away from standard design by getting rid of the hydraulic system entirely. It uses electric actuators that handle lift and tilt functions at the same time with no input lag.
These electric models come in two main types:
- Battery-Electric Models: They keep their hydraulic systems and work with existing hydraulic attachments, but flow rates stay limited to 17 gpm
- All-Electric Models: They skip hydraulics completely and need special electric attachments that are still being developed
The design is much simpler now. Electric models run with 50% fewer components than diesel ones. My research shows these machines need just one quart of eco-friendly coolant, while diesel/hydraulic machines use up 60 gallons of fluid.
The Firstgreen Industries Elise 900 sticks with traditional hydraulic systems and puts out 17 gpm flow at 2,650 PSI. This means it works with existing attachments while giving you electric benefits. The biggest problem right now is that no current electric models can handle high-flow attachments.
Control systems have gotten much better too. Today's electric skid steers come with smart software that lets operators adjust response rates and save different user profiles. You couldn't do any of this with old hydraulic systems.
Conclusion
I've compared electric and diesel skid steers and found that both types shine in different work situations. Electric models cost less to operate, need less maintenance, and produce zero emissions. These features make them perfect for indoor work and environmentally sensitive areas. They deliver instant torque and run quietly, which adds value in specialized jobs.
Diesel skid steers excel at running longer and work with all attachments. These machines prove reliable for remote sites and heavy-duty jobs that last entire shifts.
Your specific work needs should guide the choice between electric and diesel options. Electric models can reduce operating costs when your jobs allow charging breaks and don't use high-flow hydraulic attachments. Diesel units work better if you need extended runtime or often use specialized attachments.
Construction equipment keeps evolving, and both technologies will improve. Electric skid steers now stand as a real alternative to diesel power. They work best for businesses that want to cut running costs and reduce their environmental footprint.